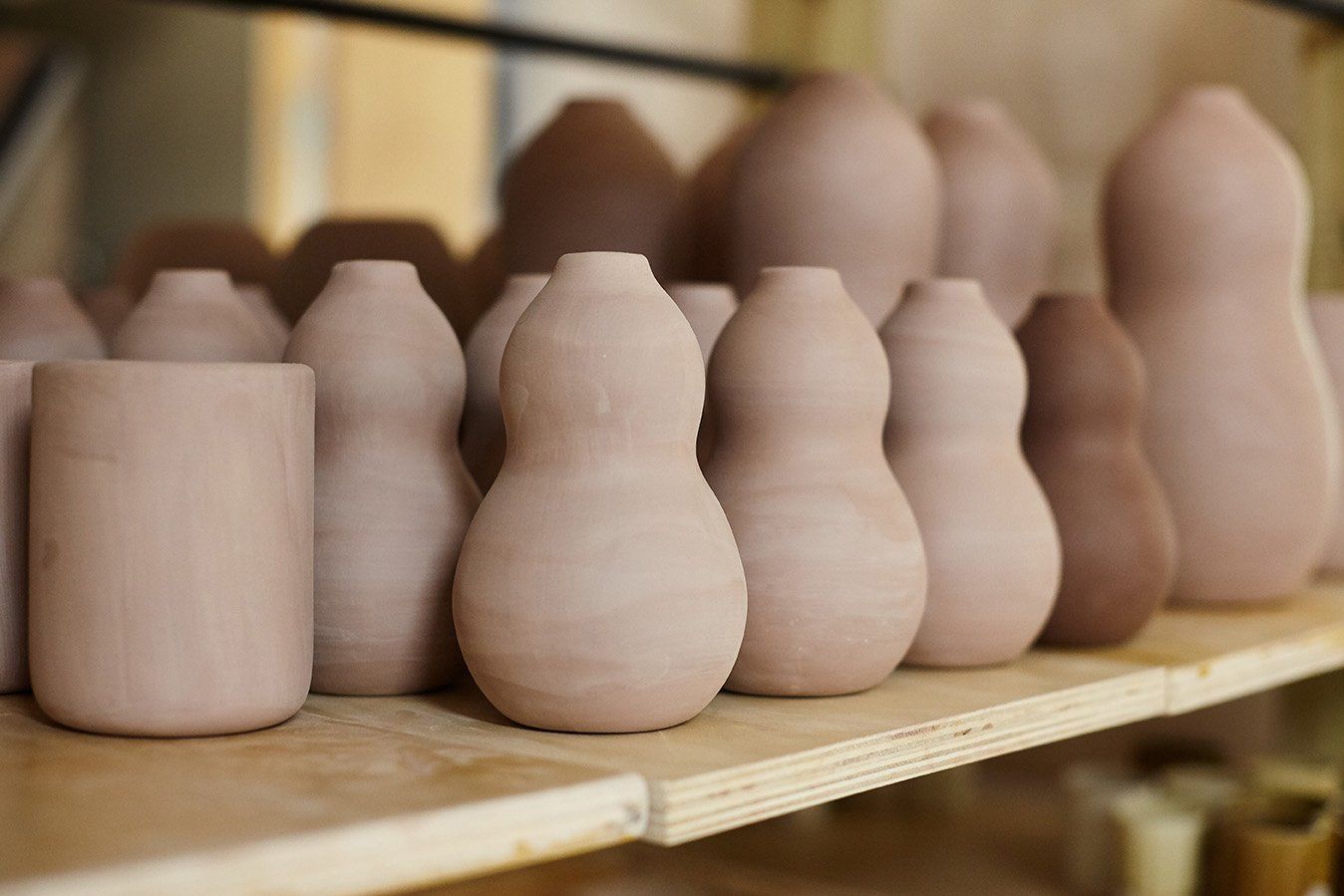
What Even Is Slipcasting?
There are so many ways to make pottery. Jiggers, wheels, ram presses, slip-casting, etc. The ceramic world is rich with tools of the trade to get things looking uniform and beautiful. Ways to make sure your plates stack up nice in the cabinet and your vases looks smooth and blemish free (except for the beautiful iron flecks, of course). Slip-casting is a tried and true ceramics technique in which you pour a liquid clay body into a plaster mold in layers to eventually create a hollow form. It’s what we’ve been working on with The Bright Angle for some time now.
I scooted over to their studio, located in Asheville’s South Slope neighborhood, to talk with Nick Moen about it. He’s been working in close quarters with Alex and John these past few months to really nail the process of perfecting our slipcast vases. Aside from that, at one point he literally told me that building a 3D printer literally from scratch is actually really easy, which goes to show how much of a mold-making genius this guy is. Anyway, touring the studio and seeing things up-close was super educational for me, and hopefully gives you all valuable insight into our process! Maybe you’ll look at your vase with new loving eyes. It’s a big, exciting project, and witnessing it all was a real treat (I think I geeked out a little too hard over the 3D printer).
East Fork: What’s was the very beginning of the process?
Nick Moen: Well, John and Cade brought over these drawings. These were the original conceptions of the vases. They drew these designs, we scanned them into the computer, then played with them. They pulled them closed and open, made the bottom wider, changed the height. This all took about a month. That’s the design part of everything. It takes a while to make it good. Then after that we 3D printed a small egg vase. This is the first model we ever printed!
Amazing! Is it plaster?
It’s 3D printed plaster with plastic in it to keep it rigid. It is then sanded down and polished.
I feel like I’m going to be just saying amazing a lot. Amazing. What’s next?
Then what we do is print it out in parts. We split the seam so we could pour the mold half and half. It makes for a nice clean pot. It’s a strategy we use a lot. A lot of people don't. They make the model and put clay up to the seam line, but it's a fussier method and harder to get it perfect.
Ah. And then?
After we make the first mold, we make the rubber molds. With these we laser cut square that we fit keys in. We then put the model down [on surface] and pour in the first mold and we are able to have something that fits evenly all around. These are the molds to make more molds.
Hm, ok. A lot of molds to make more molds. Interesting. How long does a mold last?
Kind of forever. These will be part of the archives. 10 years down the line when they make an egg vase, they can still use this one. We try to make it perfect. Strive for perfection, settle for excellence.
Nice quote. So where does the actual vase get born in all of this?
So the way it works, is we fill these with slip or liquid clay. We mix it, we take this pump and pump the slip into the molds and then we fill the molds all the way up. The longer the slip sits in the mold, the thicker the wall gets because the plaster pulls the moisture. We are casting for 80 minutes, which is a long time, pretty thick.
Very thick. What are you watching for when making these vases?
There is a few things that we’re looking for to happen. Having the clay show our desired characteristics. It being dark in color, showing iron spotting, fitting the glazes, casting, and shrinking the same amount. It’s really difficult to get all of those things to work together.
How many tests did y’all have to do?
We probably did 400-500 tests. We are still working on it, but we are almost there. The body is working now but it’s not quite as dark as we want to go. We're just getting soapstone to fit, too.
That's a lot of tests! What do you mean when you say “fit”?
So, the way that the materials work chemically is that there is a thermal expansion rate. The clay expands and contracts at different points during the firing along with the glaze. So if they mismatch, then the glaze will crack. It’s like putting a size 30 waist on a size 40 man. That’s the number one thing Alex, John and I look out for.
How many vases can you make in a day?
It depends on how many molds we have. Right now we have 40 molds. And we are filling once a day. So around 40 a day. We are able to get consistency and we are able to make an inclusive process where we can train other people to do it. It just makes sense. We make vessels, and thought it could be really fun to get John and Alex to get involved using these tools.
Is this the first time you’ve done this sort of slipcasting/mold-making process?
No, this is totally our thing. We do this for pretty much everything. One thing that sets The Bright Angle apart from other businesses, is that we are able to see concept to product really fluidly because we’ve got 3D modeling capabilities, mold-making capabilities, material science knowledge, and production capabilities. It’s all small batch and we’re pretty selective about what projects we take on. We also make our own stuff and have an online shop.
Do you ever run into problems?
Everyday. From the first steps of getting the measurements on the graph paper. Something we ran into is one lip being a little taller than the other. We made these collars to use to get the lips to all be the same thickness. You can rest it on the top and cut it so its stays round and even. Little things like that is what we like to do.
Can I see the 3d printer
*shows me 3d printer*
Here’s the 3d printer. This is the one I use primarily called The Taz. Essentially, what happens is this head goes around in a circle or whatever shape it is and pulls the shape up.
Wow. *stares lovingly* So cool.
This other one is the cadillac of printers. This build plate comes into the goo, a UV light shines an image of one layer up into the goo and then it makes it adhere. Imagine a sheet of paper that has text on it. That image shines onto the goo and then that the UV light adheres that. So, there’s a substrate in here that bonds to UV light. It bonds that layer, sticks to it, and then does another layer and so on and so forth. It’s building in layers, but this one is so precise because it uses pictures.
Amazing. Imagine being a 3D printer engineer? You’d have to be a genius.
We actually built this one and it’s not that hard. It’s essentially three components. You have some axis that moves around, something that extrudes it and a computer that tells it what to do. We’ve been testing making mug handle molds on it.
Mug handles! Cool!
The interview slowly trickled off into super esoteric talk about 3D printing which I won't bore you with. Conclusively though, after learning all of this my mind almost exploded and I became super inspired to do anything interesting at all. Sort of like that feeling when you listen to a really good podcast and you’re just amped for life. That’s how I felt when I left The Bright Angle. Thanks for helping make our vases and for the informative lesson, Nick!