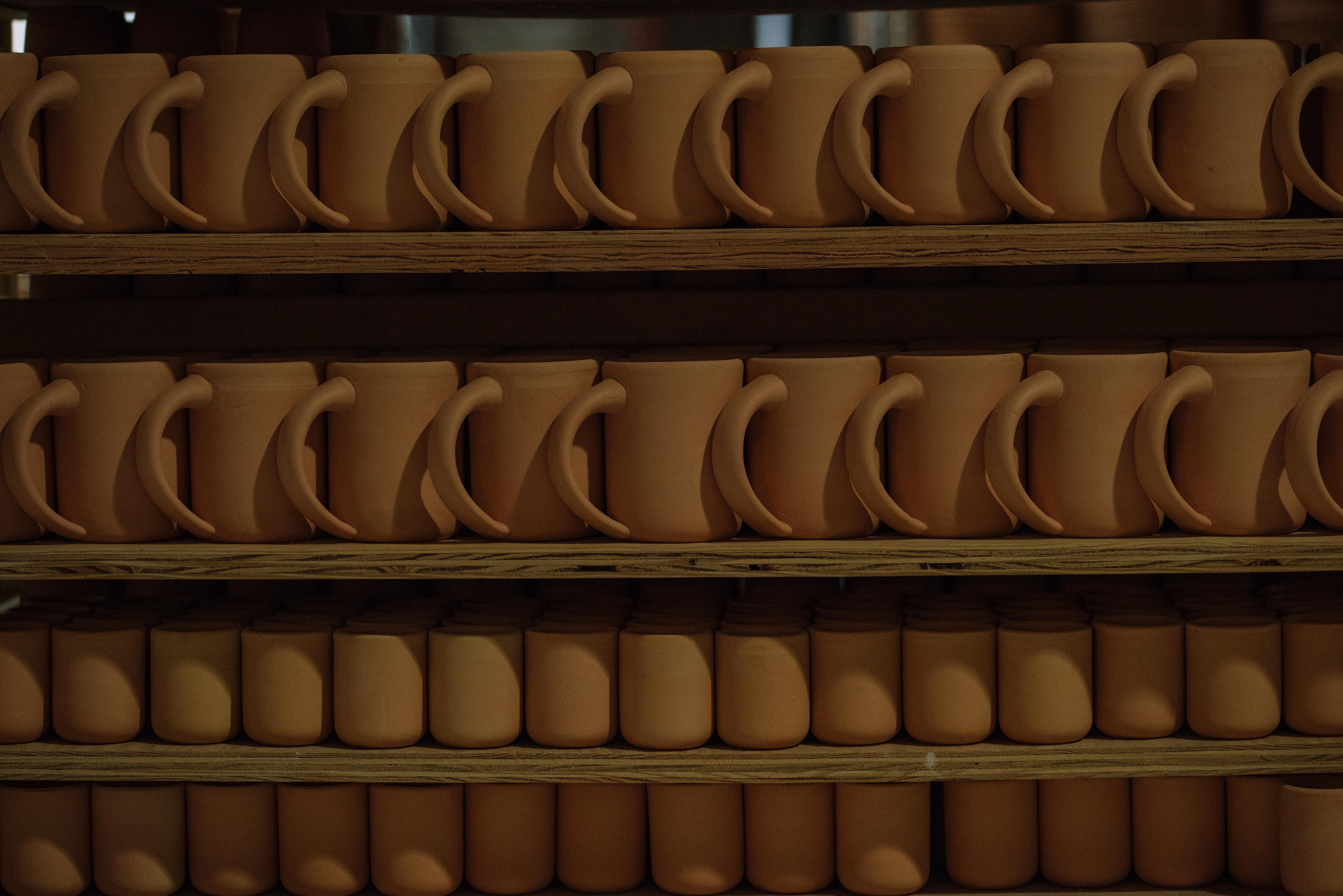
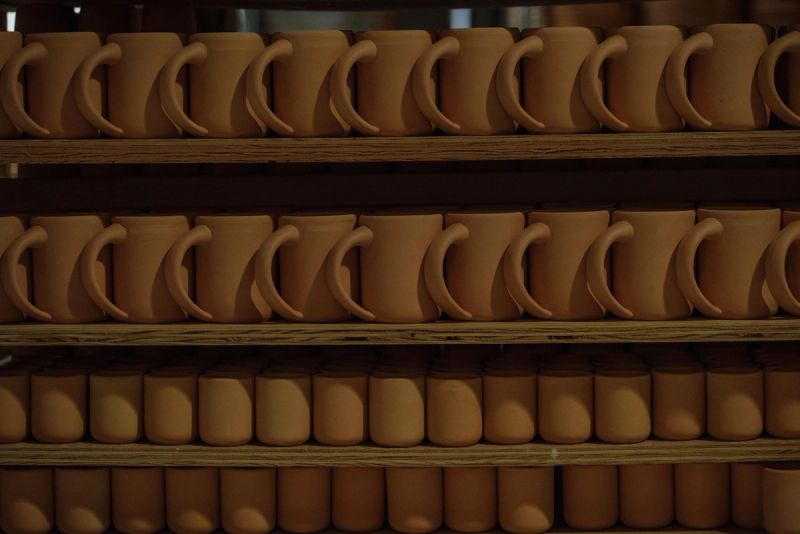
How We Got Here
While East Fork’s roots go back to an old tobacco farm turned pottery workshop tucked away in the Blue Ridge mountains, today we are one of the most technologically advanced producers of dinnerware in the United States.
We sometimes joke that we’ve worked our way through the Industrial Revolution in about five years. Early in our shift from a small country pottery toward what East Fork is today, Alex Matisse—EF’s Founder—scoured the remains of the once booming dinnerware factories across the country to find many of the machines we use today. We purchased old, forgotten equipment, often at scrap metal prices, and nursed these hulking pieces of metal back to life, learning the intricacies of a forgotten industrial art.
Our commitment to embrace technology and automation is animated by our desire to pay our manufacturing team well (3x the federal and North Carolina state minimum wage of $7.25 an hour), create safe and accessible work for all members of our community (no art degree, no previous experience with clay, no resume, no background checks required here), and create a workplace environment where people can be the fullest expression of themselves, together making and selling some of the most beautiful dinnerware in the world.
East Forks Mission:
Step 1: The Clay
We make our pottery with a blend of stoneware clays and minerals that we developed in-house and iterate on non-stop. We source our materials from the American Southeast which helps minimize our carbon footprint and keeps our products rooted to the land we call our home.
East Fork’s clay is rich in iron, as it has been since the beginning, and through a process of limiting the oxygen in the kiln during part of the firing, iron molecules are drawn to the surface of the clay resulting in the distinctive brown speckled surface our pots are known for.
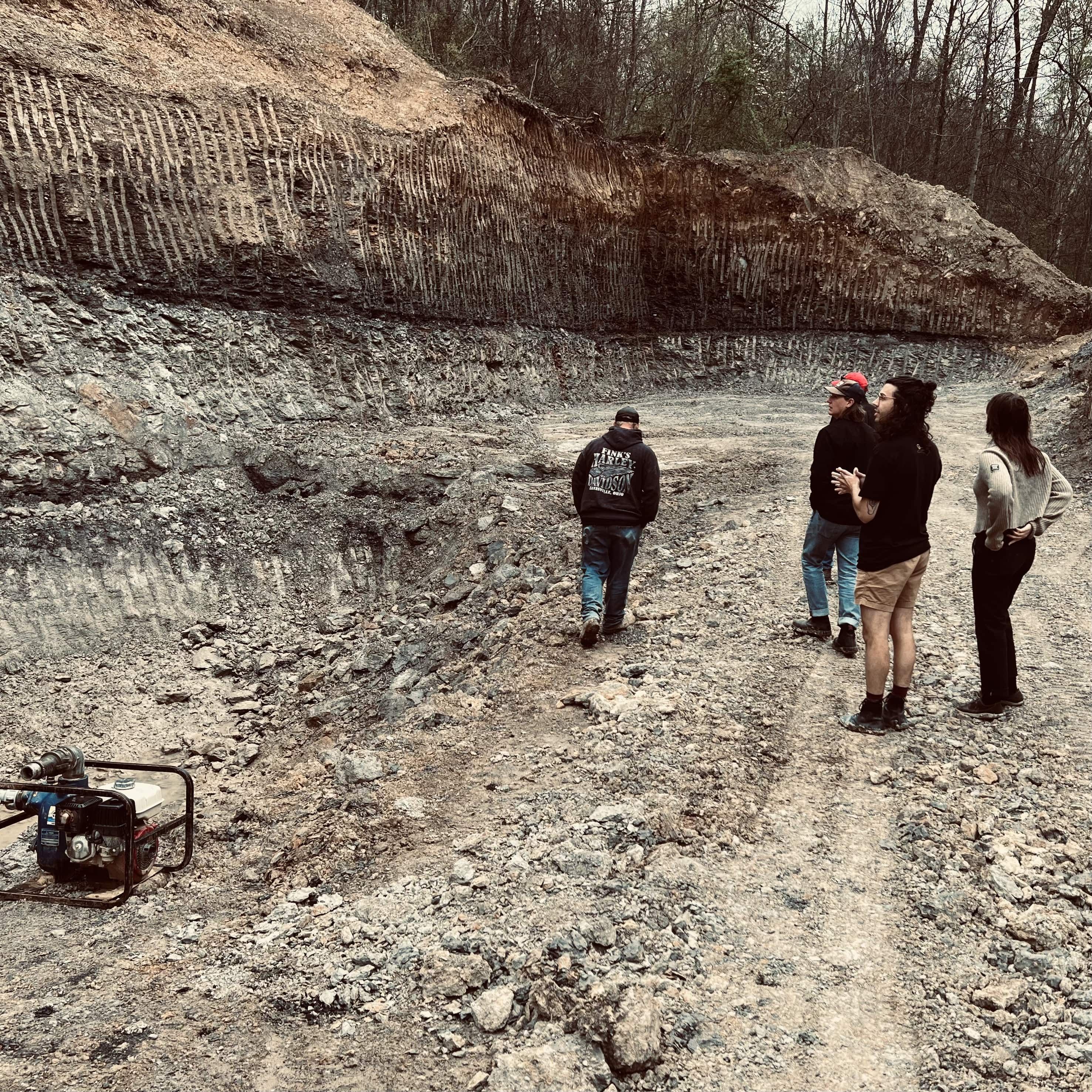
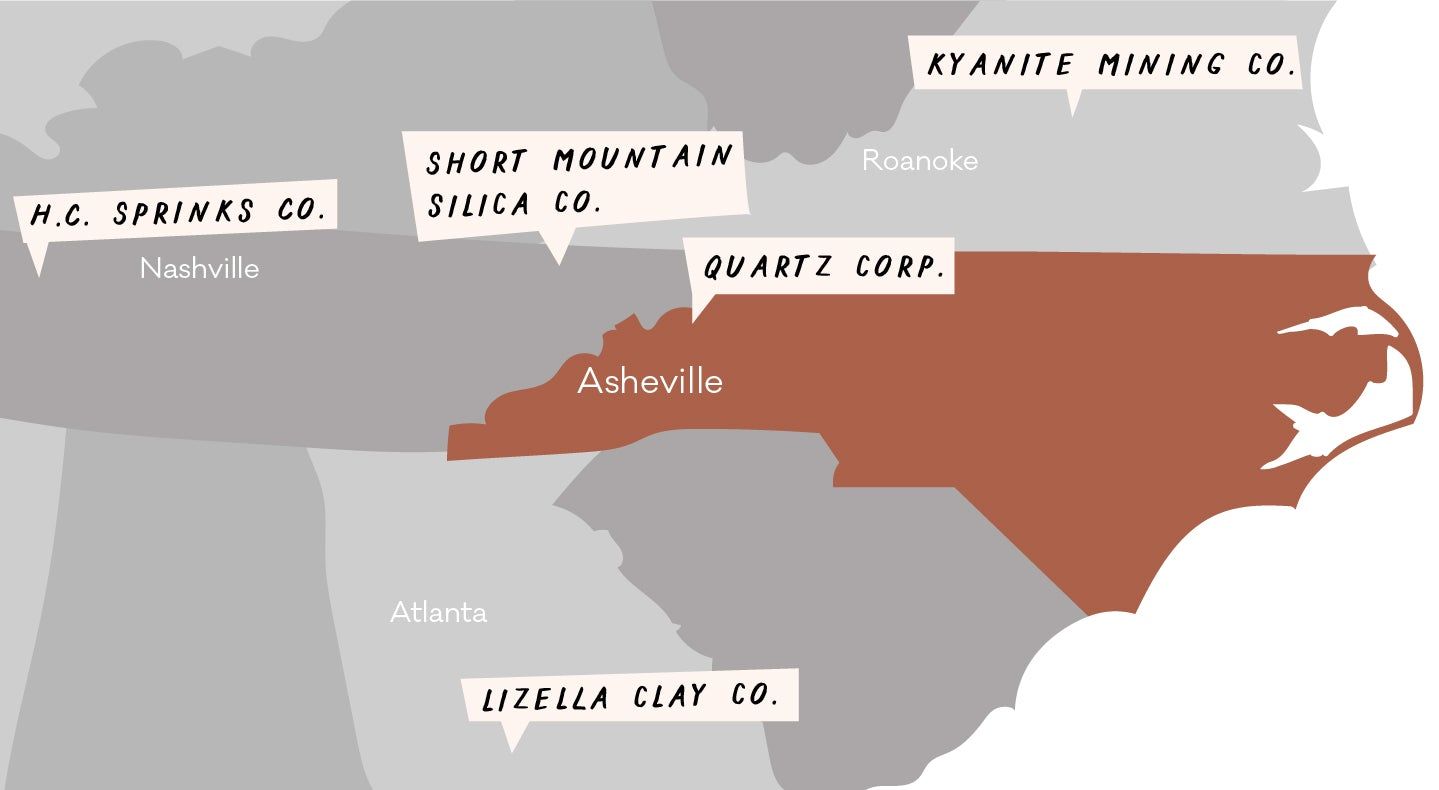
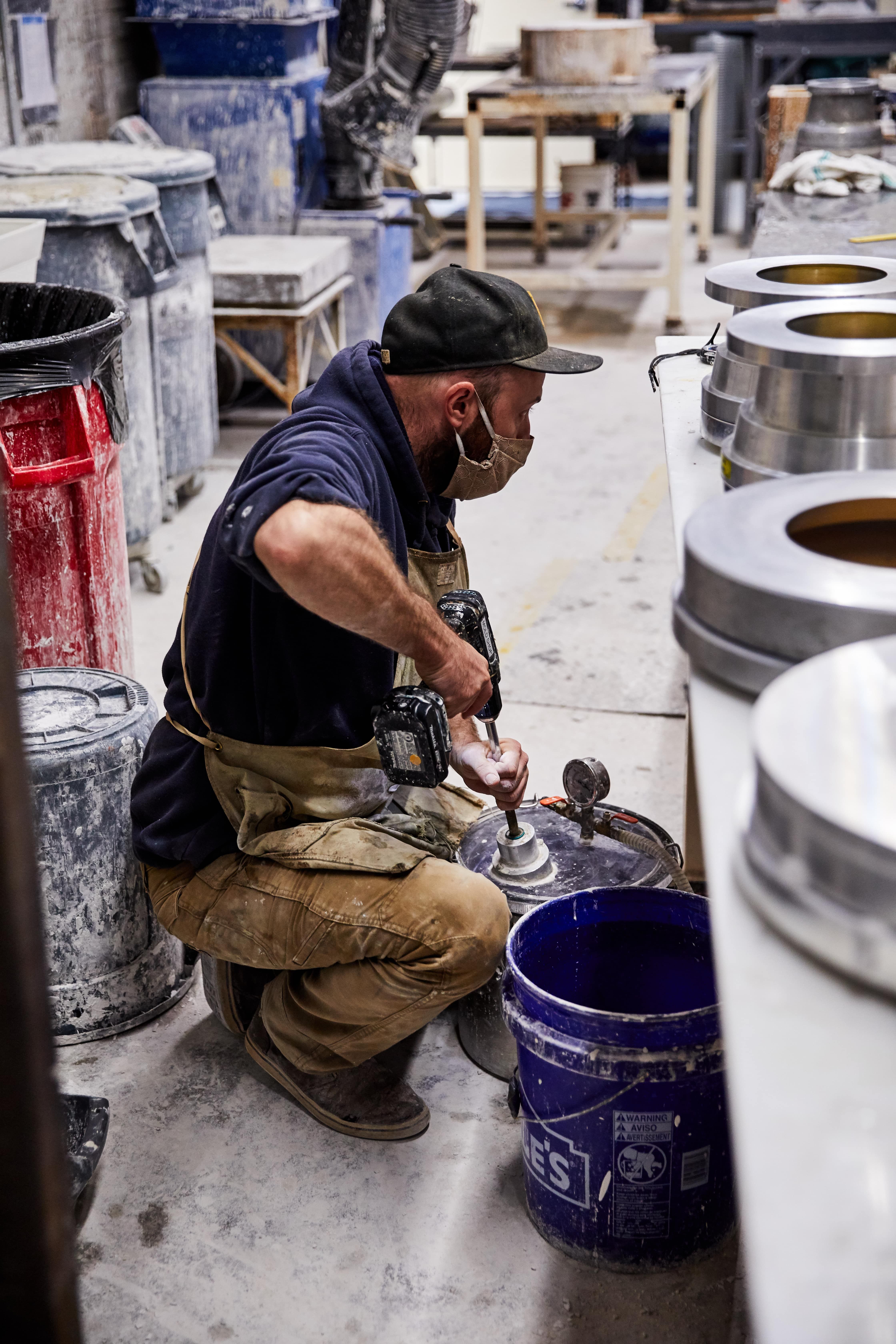
The Mold Shop
We wouldn’t be where we are without a mold shop. The art of mold and die making is one of the most specialized processes we use, and there aren’t a lot of people that know this nearly lost craft. From new product development all the way to making the “working mold sets” for each of our machines, the mold shop is a critical part of the East Fork production process.
Pugging the clay
We process the clay through a pug mill to prepare it for forming. This machine homogenizes the clay body and removes air bubbles. After the clay is pugged it passes through an automated cutter with each form having its own unique parameters. One of our pug mills was made in 1949, where it was first used by a pottery factory in Pennsylvania, then by another in Indiana. Another came to us from the Lenox China Factory in Kinston, North Carolina after the North Carolina plant was closed after new ownership chased better margins in factories overseas—a familiar story for many now defunct us dinnerware makers.
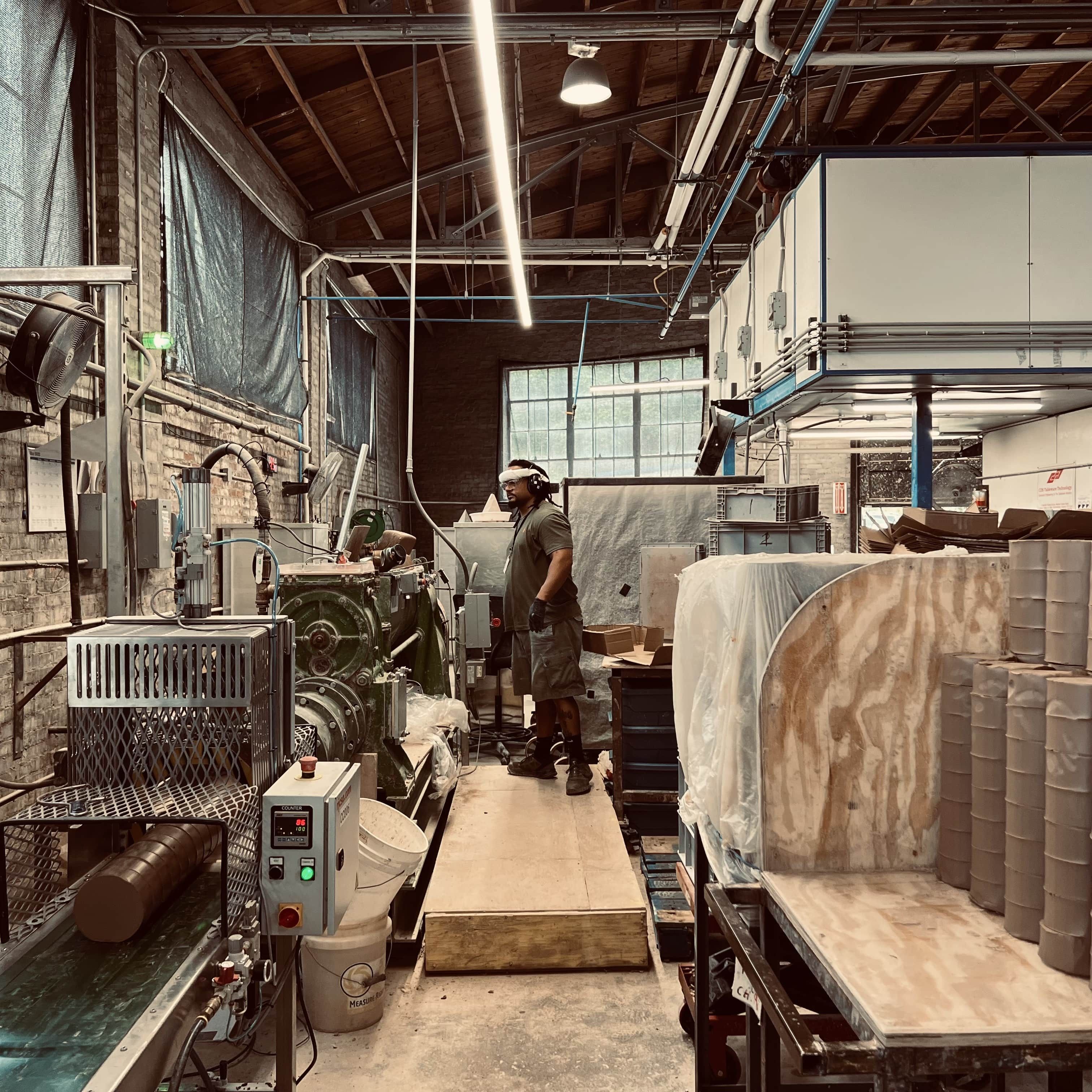
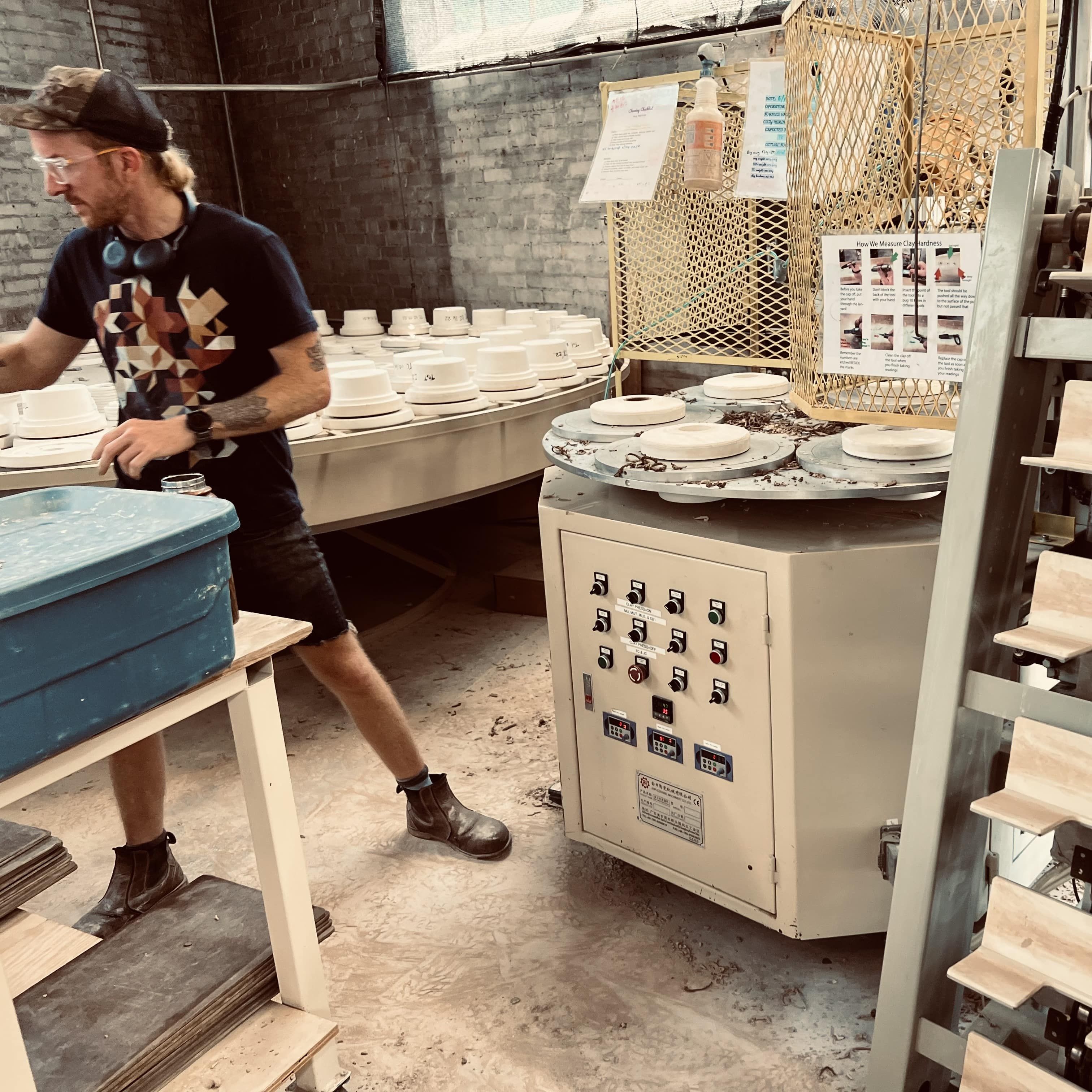
Step 2: Forming (Three Types)
Today we use three main processes to form clay into the various shapes we make. Each year we seem to introduce a new, more efficient process while other processes are retired. In our factory, where 99% of the pots we sell come from, we use ram presses, roller tools, and our newest processes: steel molds. In the next year we will introduce slip casting to make a variety of hollow shapes like vases and teapots, and further down the road we will bring in pressure casting to make mug handles and other forms that aren’t round.
Roller Tools
If you have a dinner plate in your house that was made in a factory there is a good chance it was made on a roller tool. While there are other methods to make plates in high volume, this one is tried and true and quickly forms a beautiful dinner plate between a rotating plaster mold and a steel toolhead, also rotating. We have three roller tools now, one for plates, one for mugs, cups and small bowls, and one for our larger serving bowls.
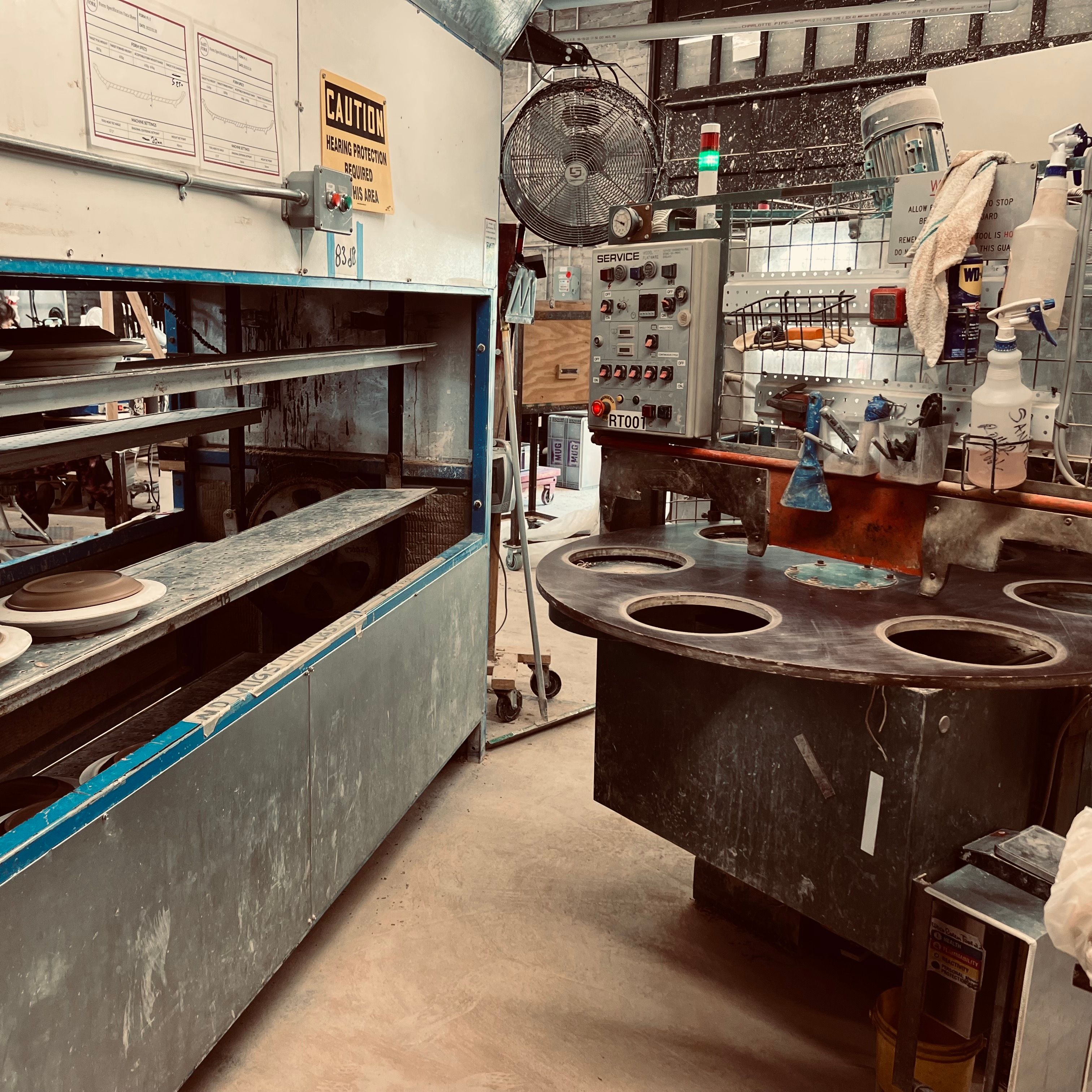
Fun Fact
The first roller tool we got was found by our founder, Alex, in a factory in Ohio that he claims looked like "a scene after the rapture". There were pieces of pottery still on the molds and the tools of the operator still sat where they had been left 10 years ago when the factory was shuttered.
Ram Pressing
The RAM press uses a large hydraulic cylinder to press two plaster dies (molds) together to form the piece. Items we do not make in high volumes and shapes that are not round are all made on the Ram Press. Most of our RAM presses are quite old and were found in various factories that had gone out of business. The largest RAM uses 135 tons of pressure and we use it to make our large serving platters and is over 15 feet tall!
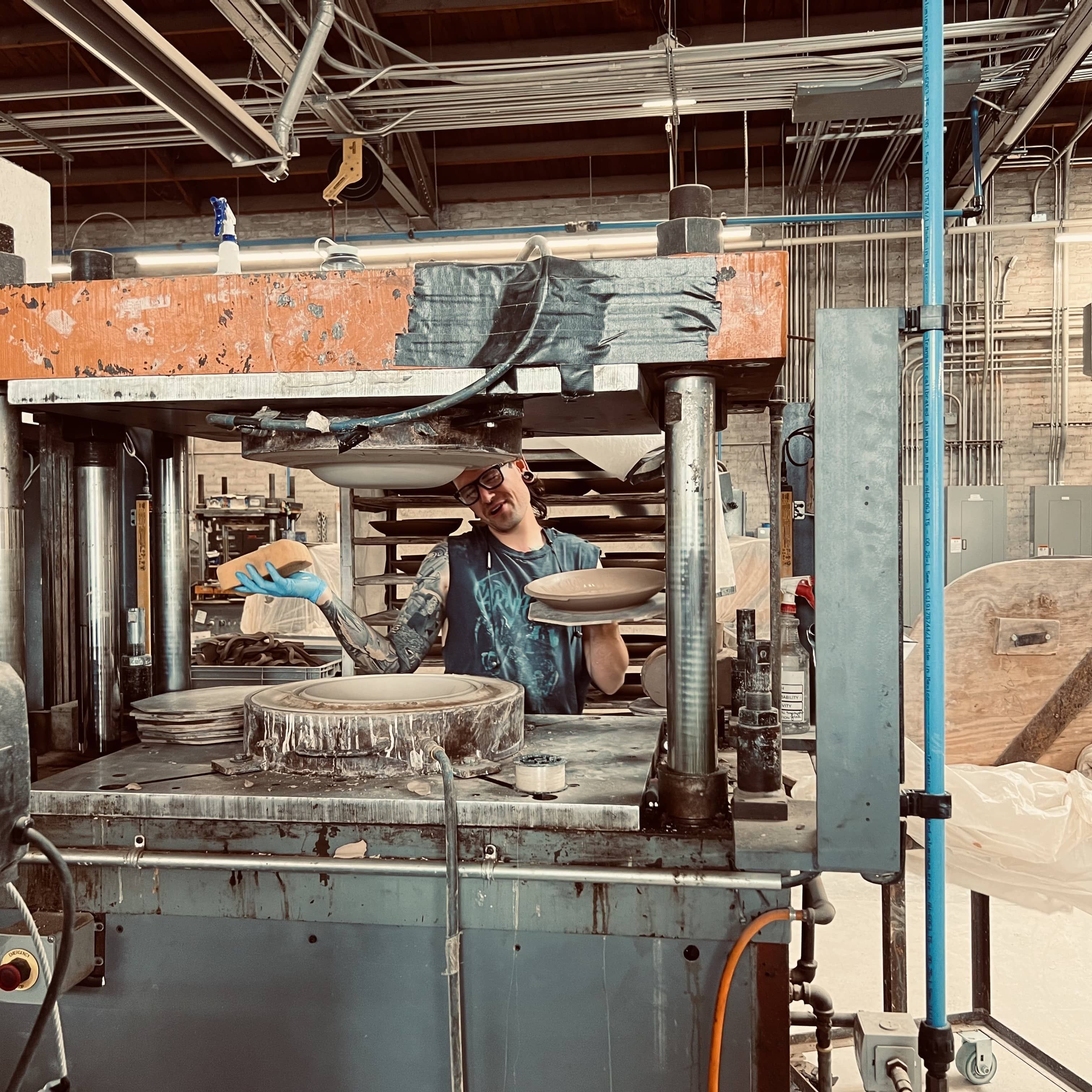
Fun Fact
The RAM press was one of the first industrial processes we adopted and is often used by potters who are trying to increase their production because it is relatively small and doesn't require a lot of other infrastructure to run the machine.
Steel Molds
The newest, fastest, and most automated process that we use is a steel mold machine from Portugal. This process has been used for many years, and is still used by factories in Ohio making crocks, and before that flowerpot producers in Georgia. Our machine is a little more advanced. A very hard pug of clay is slid between two steel molds. The top mold slides down into the bottom while rotating, forming the bowl in half a second. An extractor arm then slides over to remove the bowl, and it is trimmed and stamped with small pneumatic arms. The piece is set on a board and loaded into the dryer where after about 20 minutes it is ready for the bisque kiln.
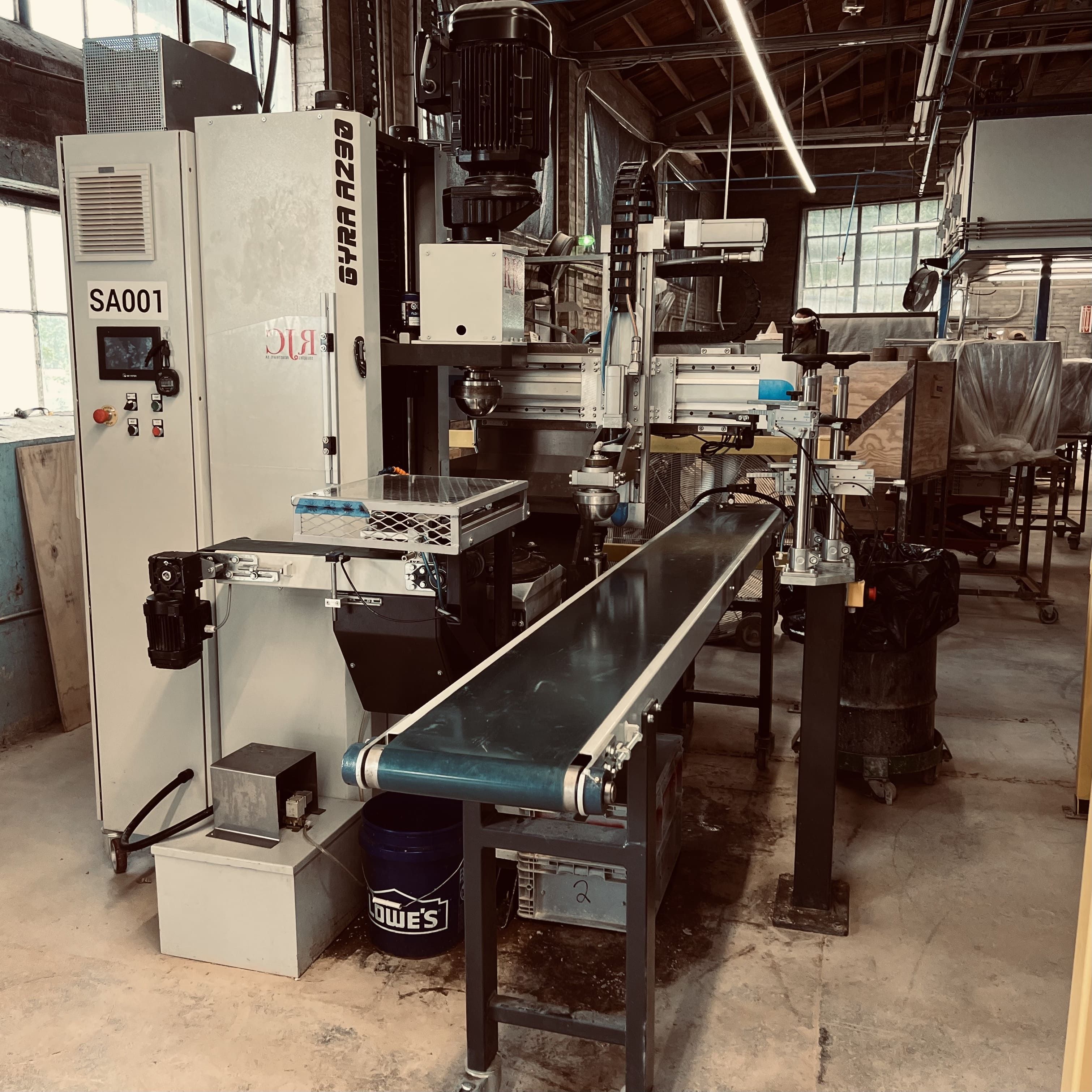
Fun Fact:
The decision to raise our minimum wage to $22/hour was made in part because we knew that this machine would introduce the level of productivity in our manufacturing to cover the cost of the $1M in new annual salaries that we were about to take on with that wage increase.
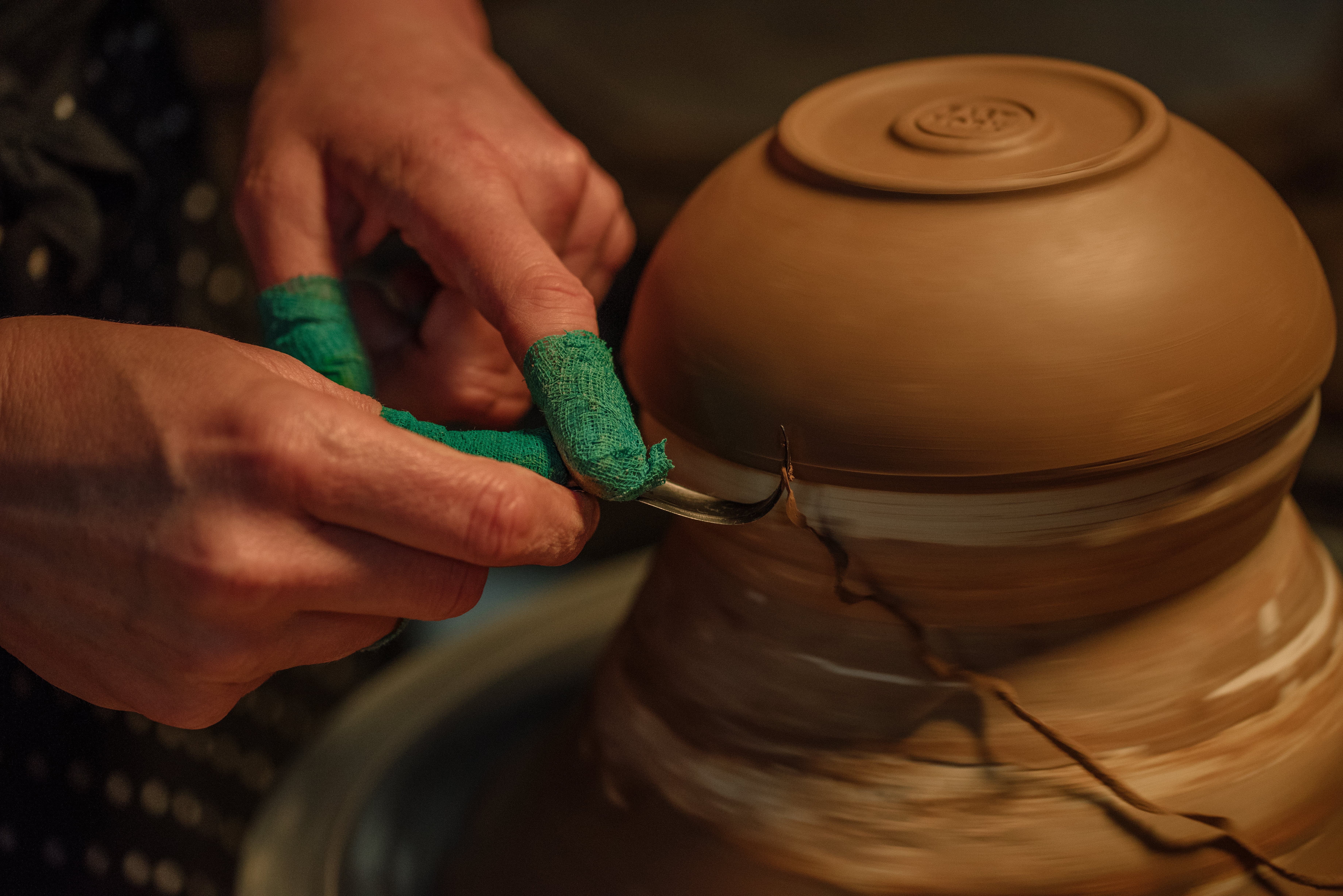
Step 3: Trimming
Once a piece is formed the “flashing” (the ragged edge of clay where the two molds met) must be removed. We currently hand trim the majority of pieces we make, however with the introduction of a new, smoother, clay we will begin to use sponge finishing machines which remove the flashing with a rotating wetted sponge.
Step 4: Drying & Bisque Firing
Different forms undergo different drying processes—some go through our overhead dryer and others are put into a large room dryer. The drying process brings our drying time down to an hour or two and eliminates warping, in contrast with traditional air drying that can take days or more in the high humidity of a North Carolina summer.
Once the pots have dried to “bone-dry,” they are fired in a lower temperature “bisque” firing overnight, ready to unload the next day and head a few miles down the road to our second factory where they are glazed, fired, quality controlled, and shipped to you.
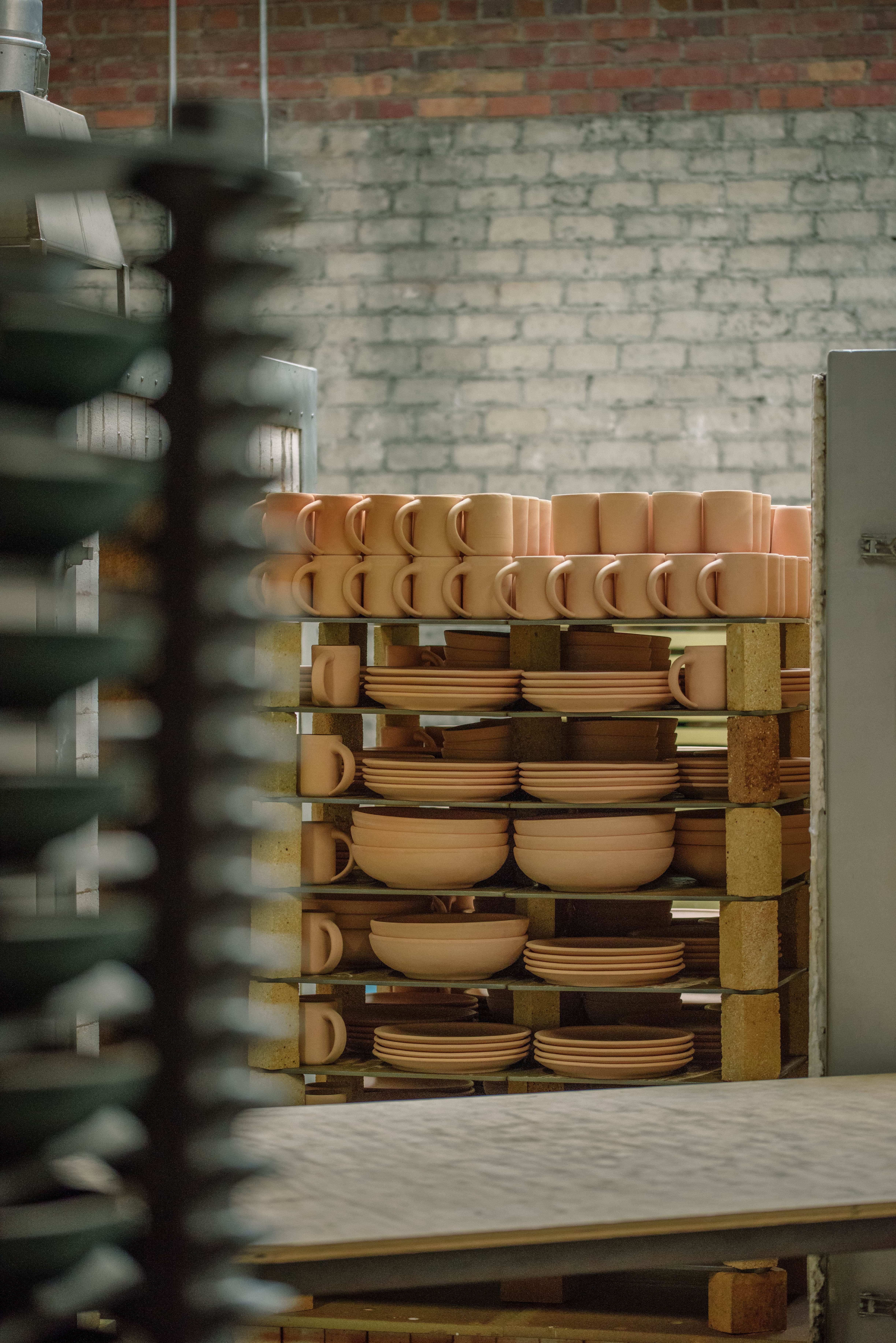
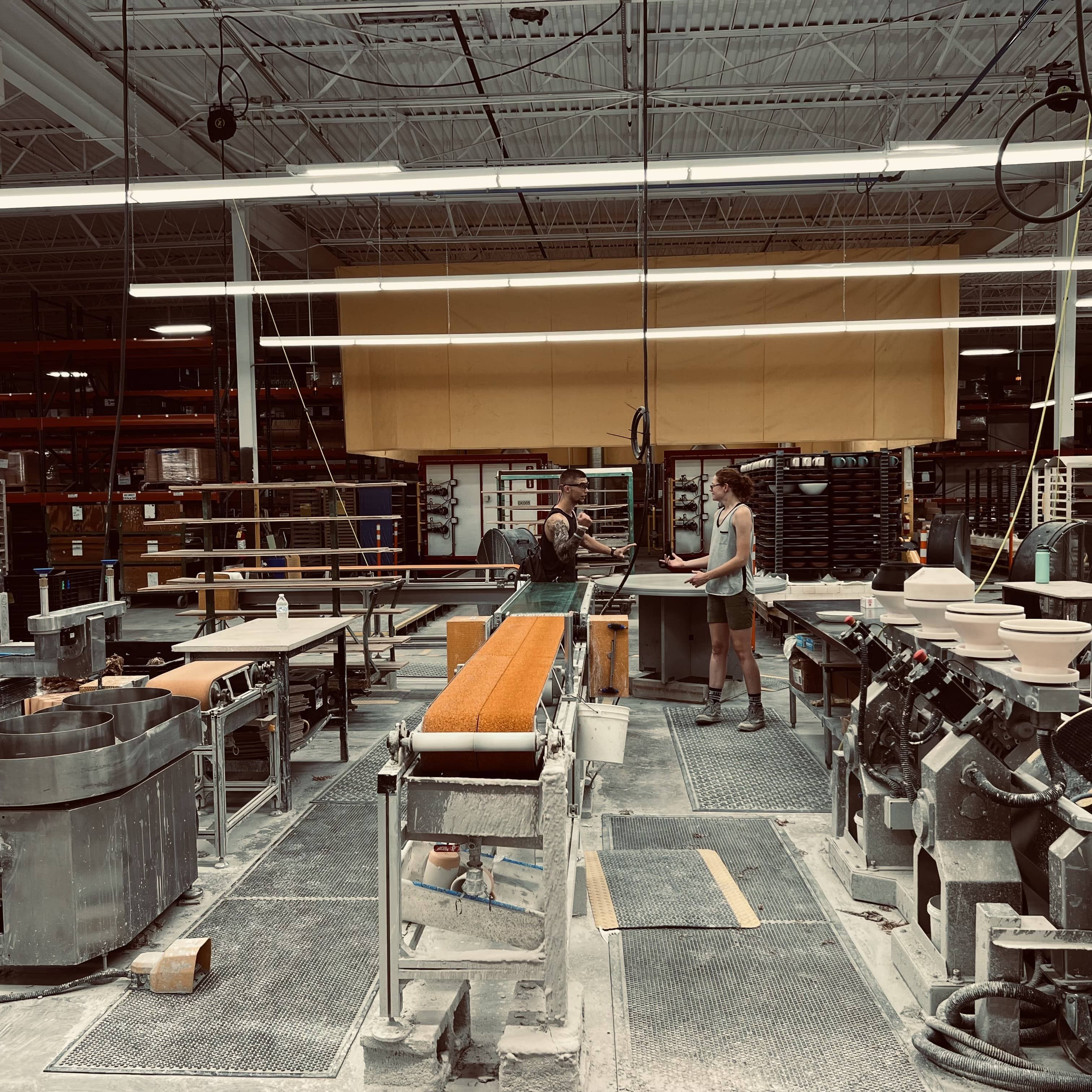
Step 5: Glazing & Glaze Firing
Once the pots finish their bisque firing, they’re ready to be glazed! All of our glazes are developed and mixed in-house. Our glaze team carefully dips each pot into the glaze and wipes the rims and feet clean to expose the clay body using a sponge belt or manually. Once the glaze dries, we load them into the glaze kiln for one final firing.
We fire the glazed pottery into our gas-fired kiln at Cone 10, a much higher temperature than bisque firing. Firing at such a high temperature gives our glazes a vitrified surface and results in pots that are consistent in color and quality from firing to firing, which creates uniform, stackable, and highly-functional dinnerware for homes and restaurants. We fire our glaze kilns full of pottery 6-7 times a week!
Meet Our Glazes
Step 6: Quality Control
After unloading our Quality Control Team separates all the pots by form and color and goes through each stack one by one. They scan for visual flaws, run their hands over the entire surface area, and feel the weight of each piece. From there, the pot is determined to be a first, second, or third. Firsts are pots that meet our highest standards, the ones that end up on our website and in our stores. Seconds have minor blemishes and imperfections; we sell them at 30% off on our website and occasionally for deeper discounts. Thirds—very wonky mishaps—never make it to customers, though many of us on the team here have amassed funny little personal collections.
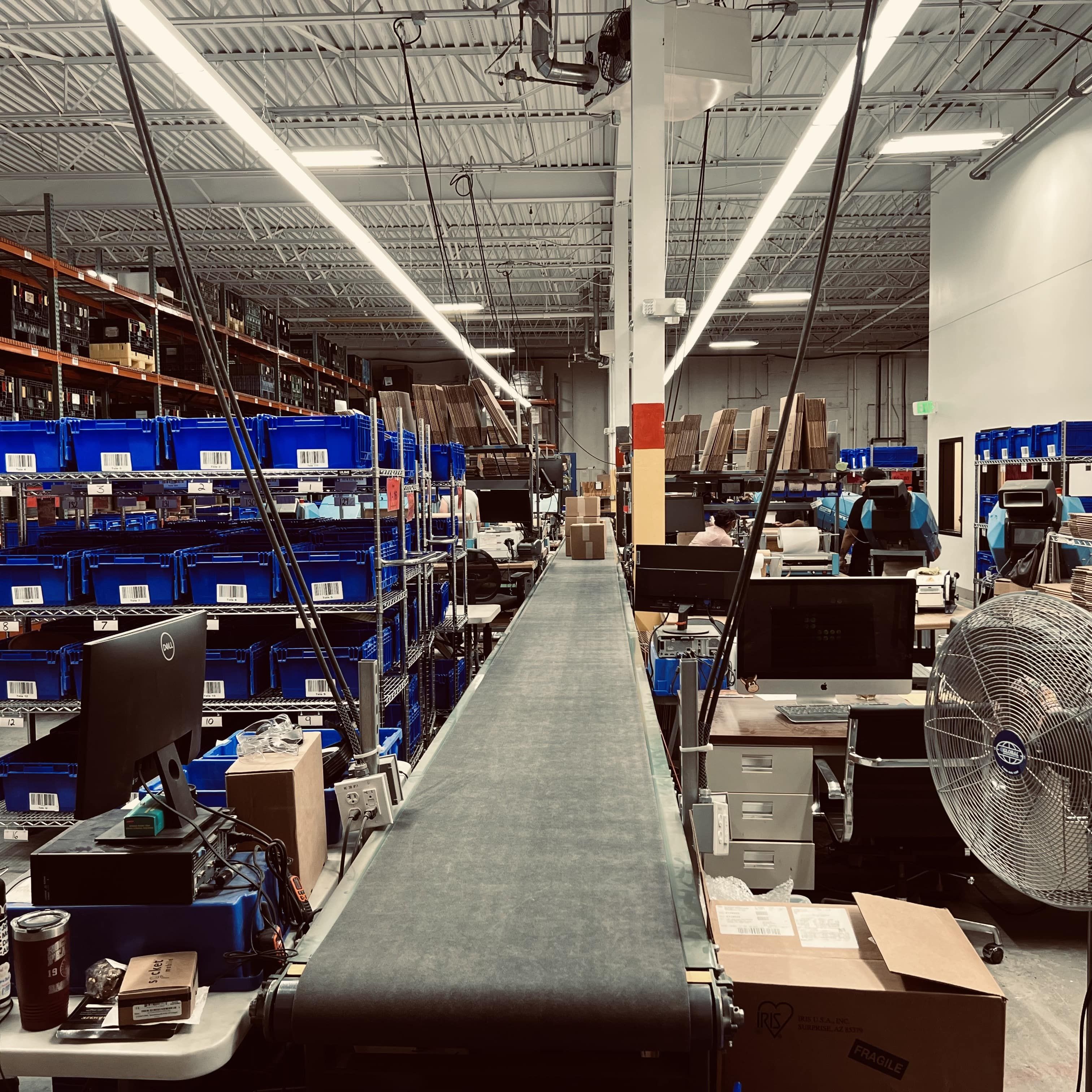
Step 7: Fulfillment
Lastly, when pottery is smooth, pristine, and clean, it is loaded onto the shelves where it waits for an unsuspecting customer to fall in love with our funny little company and place an order. A “picker” takes the piece and puts it on a cart and brings it to a pack station where our “packers” wrap it carefully in a paper alternative to bubble wrap, place it in a box, and drop it on a conveyor belt which takes it down the line, and eventually into the back of a UPS truck.
Our team takes great pride in making your pottery and being part of a grand and scrappy revival of an industry that once thrived here in the US. We thank you for your support, and hope you enjoy your dishes, bowls, and mugs for many, many years.
We make durable, dishwasher & microwave safe, and always lead-free pottery in the Blue Ridge Mountains.