
The Scoop on Coupes
Sometimes people ask us why we don’t introduce more pottery forms: different sizes of our current line-up, new dimensions for old favorite, never-before-offered things. And along with these requests sometimes comes the expectation that we can introduce these new dream products pretty quickly.
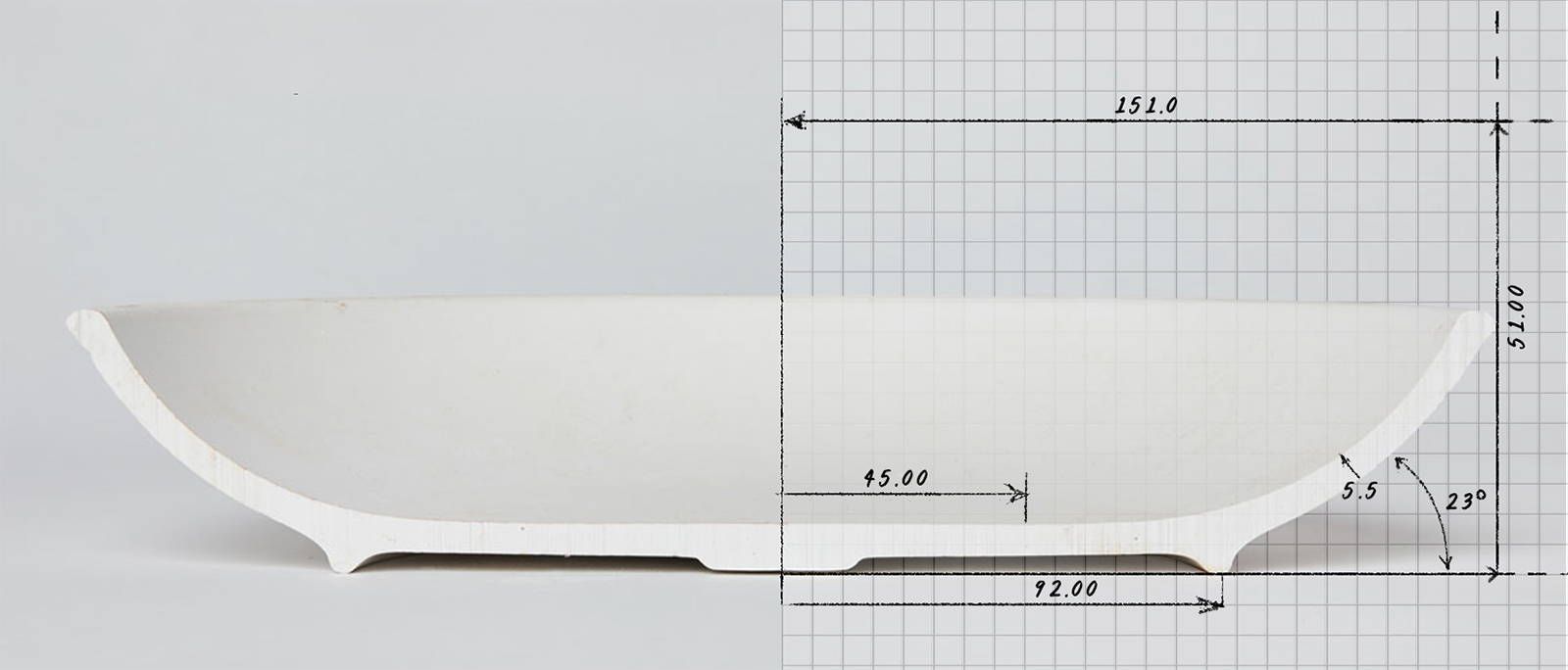
The short story is, a whole lot goes into creating a new form, and that’s even before the first piece of clay hits the factory. But it’s an interesting process.
And so, we thought we’d offer a glimpse into everything that went into the making of the newest East Fork pot: The Coupe, a form that we launched in March 2021.

First, what’s a coupe? It’s a type of car, of course, but it’s also a plate-bowl. Some describe it as a Dinner Plate with a higher wall. Others, an Everyday Bowl, but more shallow, with a diameter closer to a Weeknight Serving Bowl. But that’s the East Fork parlance—we didn’t invent the coupe. You often encounter it in restaurants because it’s great for presenting, which is to say its slosh-resistant, as saucy, strategically plated dishes make their way from the kitchen, across the dining room and to your table.
It’s good for that in your home, too, of course. The greatest distance from counter to table is never felt so profoundly that when you are trying to play it cool with a stack of crab cakes or some towering dessert like a croquembouche. But a coupe is your everyday friend, too, for times when your salad becomes a fridge-clearer, you made what you’re slyly calling “too much pasta,” or you want to bring the whole chicken or a good old side dish to the table.
In other words, when you’re standing in front of the cabinet and neither plates nor bowls feel right, but you know you don’t need a full-on platter, it’s coupes that you want. And we knew that you wanted coupes because we got lots of requests before we offered them.
Now that we’ve established that, here’s the tale of how East Fork’s coupe came into being, a coupe that will have its debut in a collaboration with Samin Nosrat in early 2021 and join our year-round glazes later in the year.
The Process Begins
Being that we’re in it for the long haul here with the Coupe as a permanent form in our pottery lineup, we needed to scale up on equipment.
In the case of coupes, we worked from pieces Alex Matisse threw a few years ago. A slight digression: some coupes from that run were used in restaurants here in Asheville and some popped up at a Seconds sale, but we never sold those coupes for real.
Fast forward to late 2019 or so.
James Snyder, our mechanical engineer, took some careful measurements off the coupes we had in our archive. Some of these coupes he cut in half.
James put the cut pots on a scanner, then used it to generate a 2D image in Fusion 360, a computer-aided design program. James then scaled the image to the correct size then a bit more to try to account for the shrinkage, warping, and trimming that are all part of the process when working with clay and kilns.
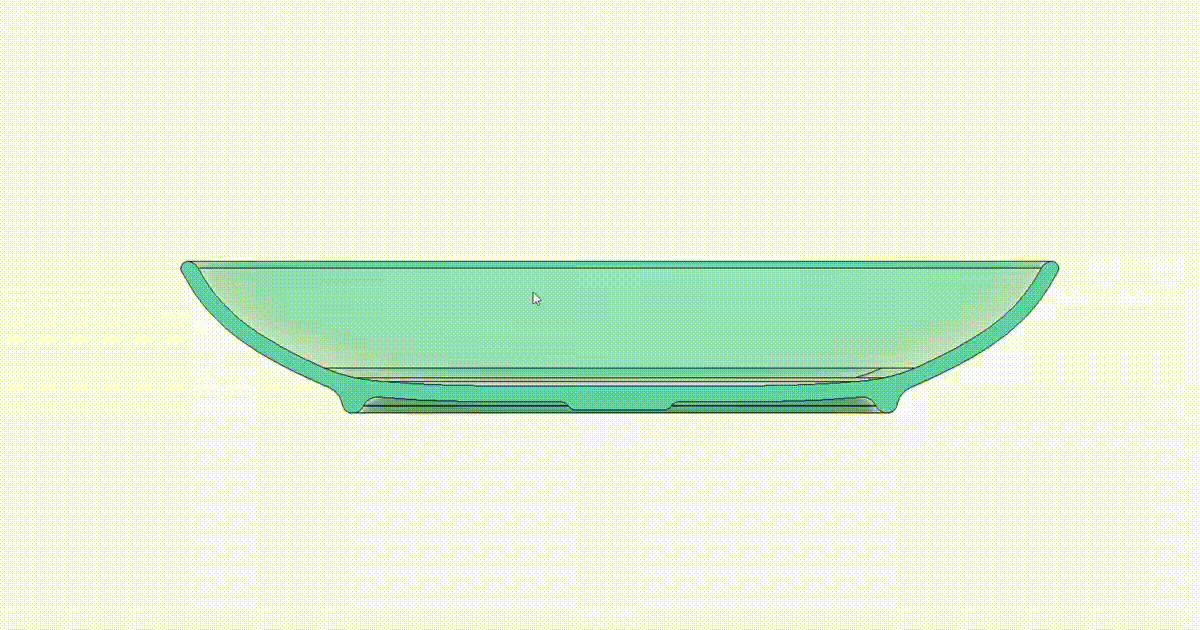
But let’s stop right here: it’s not as easy as just re-creating exactly the shape we made on the wheel. Strange stuff and we won’t deep dive too much here, but if we made a pressed version that was exactly the same shape as the thrown one, the weight distribution would be wildly different. It makes the pot feel like a totally different pot in your hands! And we think we can make improvements to the original: lighter in weight, maybe a hair bigger. James made adjustments. While we were in WFH times, he shared the renderings in video meetings, sent around some links, too.
It can be hard to visualize what screens show. Adding to that, everyone looking at the thing on their own screens made it even more difficult. That’s where even more technology came into the picture.
We had a 3D model of the coupe made on a SLS printer (that’s Selective Laser Sintering). It layers nylon powder which gets selectively fused with a small laser beam. This allows for larger prints that are very durable and fairly dimensionally accurate, according to James, who also 3D-printed the gutter. That’s the part of the mold that collects excess clay in the forming process. 3D-printed laser cutting metal profile knives were also in the mix at this stage. All part of the experiment.
Next, our mold shop made a working test die from the 3D printed components out of plaster and got feedback from the people who operated the RAM Presses on how the mold was working. (Quick RAM Press digression: it’s a machine invented in the 1940s in Columbus, Ohio, that presses clay into shapes like plates and bowls. It has two molds, one that forms the top of the piece and the other, the bottom. It gets its name from quick movement of the molds pressing the body into the required shape.)
The RAM team looked for trouble with seam lines being too big or small. They also wanted to see a specific weight range of the form coming off of the press and whether the clay released properly from the mold.They watched for any warping. The pieces made from this test die were put through the whole process of bisquing and firing, just like any other East Fork pot. Then they were sent to our creative department for feedback. When these folks we satisfied, we had a rubber master mold made, which created the plaster “working” dies that our production team will uses.
It took a lot of trial and error but if you know the Coupe, you know that this form was well worth the wait.
